18 июля — День металлурга. Трудись с душой, и металл ответит
Работники кокильно-заливочного участка ШААЗа – немногие представители большого коллектива автоагрегатовцев, кто в День металлурга 18 июля принимают поздравления с профессиональным праздником.
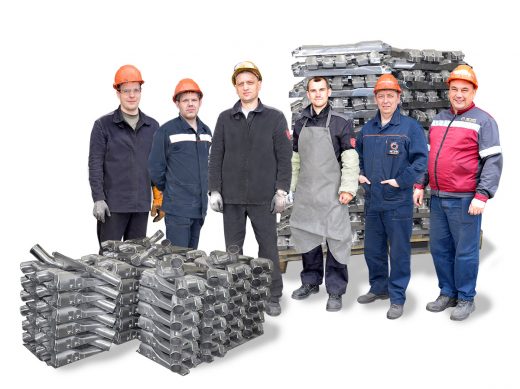
Работники кокильно-заливочного участка (слева направо): литейщик металлов и сплавов Виталий Ошурков, опиловщик фасонных отливок Олег Коуров, литейщик металлов и сплавов Сергей Зубко, электрогазосварщик Вадим Нохрин, наладчик литейных машин Егор Кузнецов, мастер кокильно-заливочного участка Алексей Гайдук
— В современной истории нашего предприятия литейное направление совсем молодое, — рассказывает мастер участка Денис Веденеев. – Когда я впервые попал в это помещение, создание участка только началось, на полу ещё лежала щебёнка. Начинали, можно сказать, с нуля, нарабатывали опыт методом проб и ошибок. Было сложно. Первое время я уходил на работу к 7.20, а возвращался домой часа в два ночи. Голову приложил к подушке, и снова на завод. Однажды не получалось устранить проблему с герметичностью бака. Что бы ни предпринимали – не выходит и всё! Пришли со вторым мастером на участок ночью, после смены, и начали проводить эксперименты. В итоге и проблему решили, и в свои силы поверили.
Сейчас кокильно-заливочный участок производства теплообменников «Ноколок» представляет собой обжитое пространство и сложившийся коллектив из тридцати человек. Здесь производят более двадцати наименований баков для алюминиевых теплообменников. Повсюду возвышаются аккуратно сложенные на поддоны алюминиевые чушки, своим холодным блеском напоминающие серебряные слитки. Завораживает процесс получения отливки, когда расплавленный металл, словно вода, заливается в форму. Дождём рассыпаются искры от шлифовальных станков, на которых отлитые и освобождённые из формы заготовки полируются до блеска.
— Всё начинается с приготовления расплава, — посвящает в секреты производства Денис Александрович. – Шихтовые материалы смешиваются и выдерживаются какое-то время в печах при температуре 1100 градусов. После этого отливаются чушки. В твёрдом состоянии они «отдыхают» одну-две недели. В это время в них идёт процесс усвоения шихтового материала, что необходимо для хорошей проливаемости деталей. После «вылежки» чушка снова отправляется в печь, плавится, и только потом переливается в литниковую систему — систему каналов и полостей, через которые подаётся в полость литьевой формы. Полученная отливка – ещё не готовое изделие. Она освобождается из системы, шлифуется и доводится до товарного вида.
Проследить производственную цепочку на участке можно всего за одну минуту. Однако сам процесс, особенно подготовительная его часть, очень трудоёмок и длителен по времени. Вникнув в тонкости, понимаешь, насколько нелёгкий это труд.
— Литьё – это специфический процесс, успешность которого складывается из множества факторов: состав, температура расплава, температурный режим в цехе и даже… настрой работника! — говорит Денис Веденеев. — Если человек трудится с душой, старается добиться результата, то и отдача от металла соответствующая. По-другому в нашем деле никак. Мы не только машиностроители, но и металлурги, поэтому и ответственность на нас двойная.
Историческая справка
Литейное дело существовало на ШААЗе с момента основания завода в 1941 году. Через шесть лет силами отдела капитального строительства небольшая литейная мастерская по производству отливок для ремонтных нужд предприятия стала цехом. Его официальным днём рождения считается 25 апреля 1947 года, когда был получен первый серый чугун.
С 1947 по 1970 годы в литейке проведены четыре реконструкции, превратившие её в комплексно-механизированное производство. В 1998 году цех перестал числиться как самостоятельное структурное подразделение, вошёл в состав управления на базе УГМех и получил название литейное производство. А в 2001 году был преобразован в литейный участок СРПУ, который работал до 2004 года.
Ирина БУЛЫГИНА, фото Ларисы ПАТРАКЕЕВОЙ